Fuel Blending: Types, Process, Benefits, Challenges, Equipment
Learn everything about fuel blending in this comprehensive guide, from types to processes, challenges, and equipments.
Fuel blending is a crucial process in modern energy production, used to create fuels that meet specific performance requirements, environmental standards, and cost-effectiveness. From gasoline to biofuels, fuel blending plays an integral role in various industries, including automotive, aviation, and the energy sector.
This guide dives deep into the concept of fuel blending, covering its types, advantages, industries’ challenges, providing professionals with a thorough understanding of this process.
Table of Contents:
- What is fuel blending?
- Types of fuel blends
- Pros and cons of fuel blending
- Operational challenges in biofuel blending
- Fuel blending process
- Fuel blending equipment
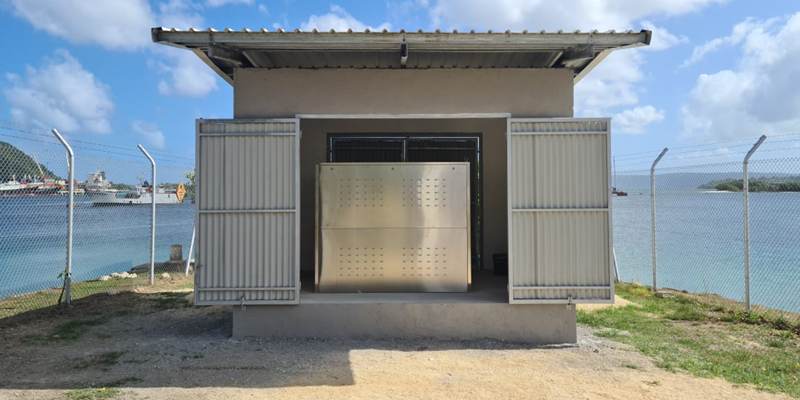
What is fuel blending?
Fuel blending is the process of mixing different fuel components to produce a final fuel product that meets the required specifications for performance, cost, and environmental impact. It allows manufacturers to create fuels that are tailored to specific needs, optimizing fuel properties such as energy content, emissions, and combustion characteristics. Fuel blending is essential not only in traditional petroleum-based fuels but also in biofuels and alternative energy sources.
Blending is performed in refineries and tank farms using various feedstocks. The goal is to create a fuel blend that delivers the best performance while minimizing costs and meeting environmental standards.
Want to learn more about fuel blending? Download our complete guide!
Types of fuel blends
Fuel blends can vary widely depending on the intended use, environmental requirements, and the availability of raw materials. Below are the most common types of fuel blends:
Gasoline blending
Gasoline blending is one of the most common types of fuel blending, as involves most of the automotive energy industry. The process involves mixing various hydrocarbons, including straight-run gasoline, reformate, and oxygenates like ethanol, to produce a final product that meets the required octane rating and vapor pressure. The blending process allows refiners and tanks farms to deliver gasoline meeting both the required fuel properties as well as the local legislation in terms of renewable origin fuel percentage.
The gasoline blending process is highly controlled and requires precise measurement of components. Small variations in the blend can have significant economic and legal implications.
Methanol & ethanol blending
Both those alcohol based blendings involve the incorporation of alcohol into gasoline or diesel fuels. Methanol is a type of alcohol that is increasingly used in alternative fuel blends due to its high oxygen content and ability to reduce carbon monoxide and hydrocarbon emissions. It is often blended with gasoline to create M85 (85% methanol and 15% gasoline) or M100 (100% methanol) for use in specially designed engines.
While methanol is a cost-effective and renewable fuel, it has lower energy content than gasoline, which can reduce the fuel economy of vehicles running on methanol blends. Additionally, methanol is corrosive, which may require modifications to engine parts and fuel infrastructure.
Ethanol blending is one of the most widely adopted forms of fuel blending worldwide, particularly in countries like the United States and Brazil. Ethanol, a renewable alcohol made from plant materials such as corn or sugarcane, is blended with gasoline to create ethanol-gasoline mixtures such as E10 (10% ethanol and 90% gasoline) and E85 (85% ethanol and 15% gasoline).
Ethanol blending helps reduce greenhouse gas emissions and reliance on fossil fuels. However, the higher volatility of ethanol can lead to challenges in engine performance, especially in colder climates where ethanol-blended fuels may cause starting difficulties.
FAME blending
FAME (Fatty Acid Methyl Ester) blending is a process where biodiesel, made from vegetable oils or animal fats, is blended with petroleum diesel to create a more environmentally friendly fuel. FAME biodiesel has several advantages, including reduced particulate emissions and a lower carbon footprint compared to conventional diesel.
However, FAME biodiesel has some challenges, such as lower oxidative stability and increased water absorption, which can lead to fuel degradation over time. Careful monitoring of fuel storage and handling is required to prevent issues with fuel quality.
HVO (Hydrotreated Vegetable Oil)
HVO is a type of renewable diesel made by hydroprocessing vegetable oils or animal fats to create a synthetic fuel. HVO is chemically identical to petroleum-based diesel but has a much lower environmental impact. It is often used in high-performance engines and can be blended with conventional diesel to reduce carbon emissions.
HVO is considered one of the most promising biofuels due to its high energy density and compatibility with existing diesel infrastructure. It is a key component in the push for sustainable aviation fuels and other heavy-duty transportation sectors.
Diesel fuel blending
Diesel fuel blending involves mixing various components such as crude oil distillates, biodiesel, and synthetic fuels to produce a final diesel blend that meets performance and emission standards. Diesel blending ensures that the final product has the necessary cetane number, flash point, and sulfur content to meet regional regulatory requirements. By blending lower-cost or renewable components, refiners can optimize their production costs while reducing the carbon footprint of diesel fuels.
Bioethanol blending
Bioethanol blending is the process of incorporating bioethanol, a renewable fuel derived from plant matter, into conventional gasoline. This blend reduces the environmental impact of gasoline by lowering its carbon intensity. Bioethanol helps lower emissions of particulate matter, carbon monoxide, and volatile organic compounds, making it a popular choice in environmentally conscious regions. However, bioethanol blending can present challenges related to water absorption and fuel stability, which require careful management to ensure optimal fuel quality.
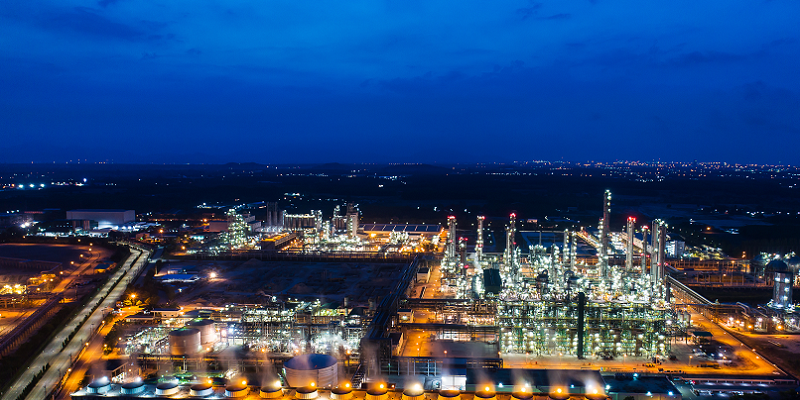
Biodiesel blending
Biodiesel blending is the process of mixing biodiesel with petroleum diesel to create a fuel blend that maintains the performance characteristics of traditional diesel while reducing emissions. Biodiesel, made from renewable sources like vegetable oils or animal fats, is blended to reduce particulate emissions, improve engine lubrication, and reduce dependency on fossil fuels. However, biodiesel blends can face challenges, including lower oxidative stability and increased water absorption, requiring specific storage and handling practices to prevent fuel degradation.
SAF blending
Sustainable Aviation Fuel (SAF) is a renewable alternative to conventional jet fuel, significantly reducing carbon emissions in aviation. Typically blended up to 50% with fossil jet fuel, SAF maintains performance while lowering lifecycle greenhouse gases. The blending process ensures compatibility with existing aircraft engines and infrastructure, requiring no modifications. As global demand for greener air travel rises, SAF represents a key solution for decarbonizing the aviation industry.
Pros and cons of fuel blending
Fuel blending offers several advantages, but it also comes with certain challenges. Here’s a breakdown of the pros and cons:
Pros:
- Environmental benefits: blending biofuels like ethanol and biodiesel helps reduce greenhouse gas emissions and reliance on fossil fuels.
- Cost efficiency: by blending cheaper feedstocks, such as butane or ethanol, refiners can lower production costs while maintaining fuel quality.
- Enhanced performance: blending allows fuel producers to meet specific performance criteria, such as octane ratings or cetane numbers, which improve engine efficiency and reduce emissions.
Learn more — Synthetic and Biofuel Blending: Advancing Sustainability in Energy Solutions
Cons:
- Storage and stability issues: some biofuels, particularly FAME, can degrade over time, leading to storage and stability problems.
- Corrosion risks: alcohol-based blends, such as ethanol and methanol, can be corrosive to engine components and fuel infrastructure.
- Increased fuel economy challenges: certain fuel blends, such as methanol, have lower energy content, which can reduce fuel economy for vehicles.
Operational challenges in biofuel blending
Blending biofuels presents unique challenges due to the variability in feedstock quality, storage issues, and regulatory requirements. Key operational challenges include:
- Quality control: ensuring that the final blend meets all performance and environmental standards requires precise monitoring and control of the blending process.
- Equipment maintenance: some biofuels, particularly FAME, can cause corrosion and clogging in equipment. Regular maintenance and the use of specialized equipment are necessary to ensure efficient blending operations.
Supply chain management: the availability of biofuels can fluctuate based on agricultural yields and market conditions. This creates supply chain challenges for producers who rely on consistent feedstock availability.
Fuel blending process
The fuel blending process typically involves the following steps:
- Selection of components: based on the required fuel specifications, various fuel components are selected for blending. These can include gasoline, ethanol, biodiesel, or other additives.
- Measurement and mixing: precise measurements of each component are taken using advanced flow meters. The components are then blended in the correct proportions.
- Quality control: samples of the blended fuel are tested to ensure they meet the required specifications, such as octane or cetane levels.
Storage and distribution: the final blended fuel is stored in tanks before being distributed to customers or refueling stations.
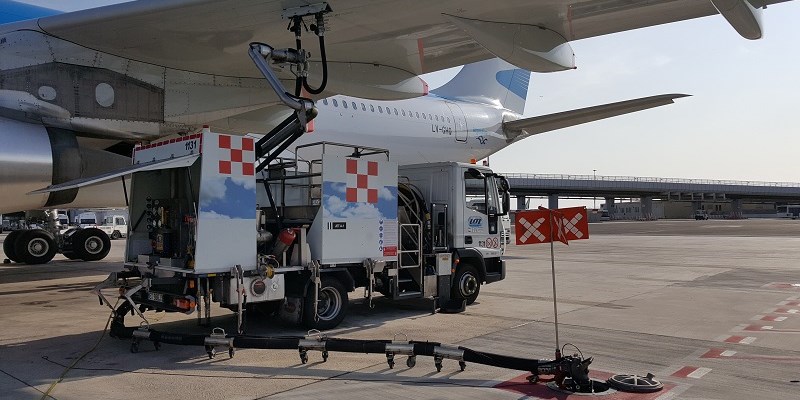
Fuel blending equipment
Fuel blending requires specialized equipment to ensure accuracy and efficiency. Key pieces of equipment include:
Electronic controllers
Electronic controllers are crucial tools used for precise measurement and monitoring of flow during the blending process. These controllers are designed to offer high accuracy and reliability in tracking the volume of fuel being blended. Electronic counters are particularly useful in ensuring that each component is added in the correct quantity, preventing errors that could result in off-spec fuel. They are also employed for totalizing purposes, enabling operators to track the total amount of fuel blended over a specific period.
PD meters
Positive Displacement (PD) meters are widely used in fuel blending operations due to their precision in measuring flow rates. These meters operate by capturing a specific volume of liquid in a chamber, ensuring accurate and repeatable measurements of fuel components.
PD meters are ideal for applications where consistent and precise flow measurement is crucial, such as blending biodiesel or ethanol with petroleum products. The use of PD meters allows refiners to meet exact blend specifications while maintaining efficiency in the blending process. Discover more about ISOIL expertise as a PD meter manufacturer!
Conclusion
Fuel blending is a vital process in the production of high-quality fuels that meet performance and environmental standards. Whether blending ethanol with gasoline, fuel blending enables the creation of cleaner, more efficient fuels for a variety of applications. Despite its challenges, such as equipment maintenance and quality control, the benefits of fuel blending far outweigh the drawbacks, making it a cornerstone of sustainable energy solutions.
For professionals in the energy and fuel industries, understanding the types, processes, and operational challenges of fuel blending is essential for optimizing production and reducing costs.
Contact us
Contact us for more informations about our services and products
Form sent successfully
Error