Oil Terminal - Tank Truck Loading
Tank Truck Loading Procedures in Oil Terminals: a Case Study
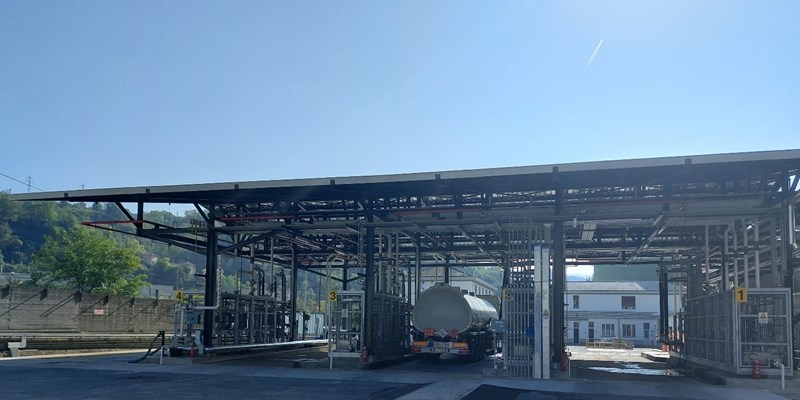
Tank truck loading in oil terminals is a common and critical procedure that involves transferring oil products from storage tanks within the terminal to the cargo tanks of tank trucks.
This process requires precision and safety to ensure efficient and secure handling of oil products.
Topics:
- Tank Truck Loading procedur step by step
- Case Study: Tank Truck Loading in an Italian Oil Terminal
- Advantages of Skid and Terminal Automation Systems
- Tank Truck Loading Operations: Management and Documentation
- ISOIL solution and project to meet these needs in tank truck loading
- Custom Solutions for Your Tank Truck Loading Procedure
Tank Truck Loading in the Oil Sector: Steps and Procedures
Tank truck loading in the oil sector follows a structured process to ensure safety, accuracy, and efficiency. The key steps involved are:
-
Truck Positioning and Grounding: the tank truck is properly positioned at the loading bay, and a grounding system is connected to prevent static electricity buildup, reducing the risk of fire or explosion.
-
Driver Identification and Authorization: the driver is identified through a badge or fingerprint system, and loading authorization is granted based on product specifications and terminal procedures.
-
Connection to the Loading Arm: the truck’s cargo tank is securely connected to the loading arm, which transfers the oil product from the terminal’s storage tank to the truck.
-
Product Measurement and Control: precise measurement systems monitor the volume and quality of the oil being loaded, ensuring that it meets specifications. Additive injection or blending can also occur at this stage, depending on the product type.
-
Loading Process: the loading system, often automated, controls the flow rate of the oil product into the truck, using anti-overfill systems to prevent spills and maintain safety.
-
Documentation and Verification: once loading is complete, the system generates documentation that includes the product type, quantity, and other relevant data. This information is sent to both the driver and the terminal operator.
-
Truck Disconnection and Final Checks: after the loading arm is disconnected, final safety checks are performed to ensure no leaks or spills. The driver is cleared to leave the terminal once all procedures are verified.
This systematic process ensures that tank truck loading is carried out safely, accurately, and in compliance with industry standards.
Case Study: Tank Truck Loading in an Italian Oil Terminal
Our client, a major consortium of leading Italian oil companies, needed to perform reliable tank truck loading operations at an oil depot. This process also included in-line additive/denaturant injection and required a comprehensive loading management system to oversee and control the entire operation.
The depot receives large quantities of various oil products from ship tankers and it then distributes the final products to numerous gas stations and industrial users across northern Italy.
Key considerations in this scenario included:
- Ensuring Safe Handling: all oil products are potentially hazardous materials. Proper handling is essential to prevent spills, leaks, and sparks that could pose risks to human health and the environment.
- Managing Large Quantities with Accurate Measurement: accurate measurement of both volume and quality is crucial to grant that the final product meets the necessary specifications, to ensure proper tracking, and to record transaction data.
- Protecting Measuring Systems: preventing unauthorized transactions is critical to safeguard system integrity.
- In-Line Additive and Denaturant Injection: the consortium's partner oil companies required diesel and gasoline pre-mixed with additives for enhanced product performance. Additionally, the Italian market allows for in-line denaturant injection for specific products with subsidized excise duties, such as agricultural diesel and heating oil, provided that real-time control instrumentation is used.
- Ensuring Precise Control of the Loading Procedure: Accurate control over the entire tank truck loading process is essential to ensure product quality and compliance with safety standards.
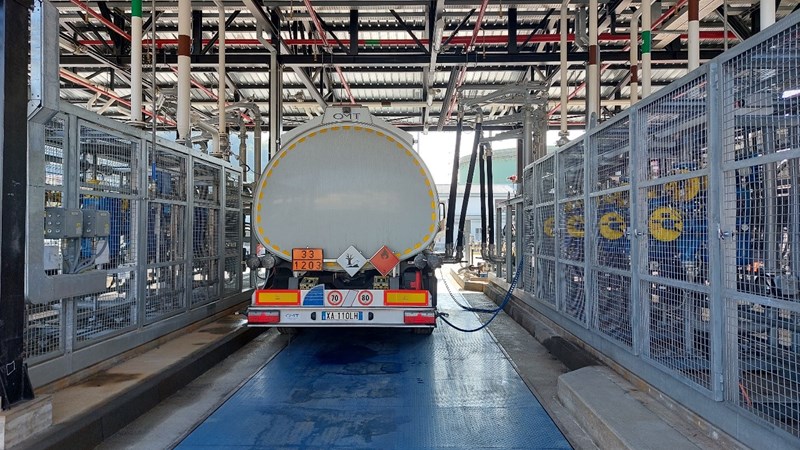
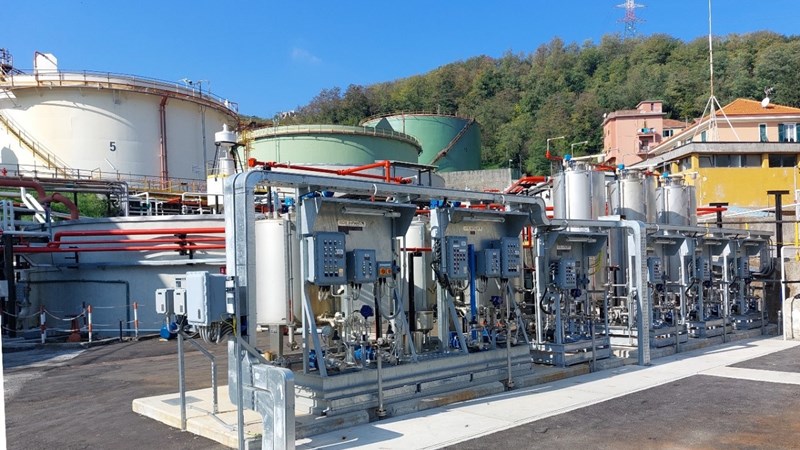
Oil Terminal - Additive Injection Skids
Advantages of Skid and Terminal Automation Systems
The skid-based approach offers significant advantages for tank truck loading procedures, including easy and fast installation. It’s particularly beneficial for projects with multiple construction phases, minimizing the need for extensive welding and civil works on-site.
Additionally, the piping and electrical connections have been prearranged to enable future blending with bioethanol in all loading arms dedicated to petrol. This project, scheduled for 2024, will also include the supply of additional measuring systems.
For information about our solutions for oil terminals, contact us!
Contact us
ISOIL solution and project to meet these needs in tank truck loading
To address such needs ISOIL Impianti designed and provided a custom-made solution including the following:
- 4 loading skids, one for each loading bay with BMV/FM p.d. meter, strainer air separator, pulse emitter, ISOVALVE automatic valve, PT100 thermoresistance, and loading bay terminal to grant precise measurement, efficient air elimination and process management and monitoring;
- A total of 18 loading arms to load tank trucks and manage the different products;
- Each measuring system installed on the skids was MID compliant;
- Each skid was provided with MT40 Grounding System to prevent the accumulation of static charges on the tank truck and reduce the risk of shock hazards;
- Anti-overfilling system to prevent spilling of product;
- Each skid was mounted inside a stainless-steel cage with lock to avoid unauthorized transactions;
- IB2 injection blocks managed by a VEGA 3 flow computer;
- 4 additive injection skids (2 for diesel oil and 2 for petrol) and 1 additive injection skid with double circuit and tank (one for agricultural diesel and one for heating oil).
Tank Truck Loading Operations: Management and Documentation
Supervision and documentation of the tank truck loading procedure are crucial to ensuring that products meet necessary specifications and that data is accurately tracked and recorded.
To achieve this, we customized a load supervision system that includes:
- Servers and operator workstations with PCs.
- A booking area with a touch screen totem and PC for driver identification via fingerprint.
- A camera system to read truck number plates at the parking exit gate for loading/unloading.
- A connection to transmit necessary information to the software managing the loading area.
- A panel PC to validate document collection, 1 PC, and 2 RFID badge readers for bidirectional turnstile entry/exit control.
- A badge reader for drivers accessing the depot for biodiesel unloading.
Custom Solutions for Your Tank Truck Loading Procedure
As a leading solution provider, ISOIL can assist in designing, customizing, and installing tank truck loading systems that best meet your specific needs, ensuring safety, efficiency, and compliance with industry standards.
Contact us for more information about our services and products
Form sent successfully
Error